How to Keep Your Truck's Electrical System Running Smoothly
Regular truck electrical system maintenance prevents unexpected failures. Learn how to inspect batteries, alternators, wiring, and fuses to keep your truck running smoothly.
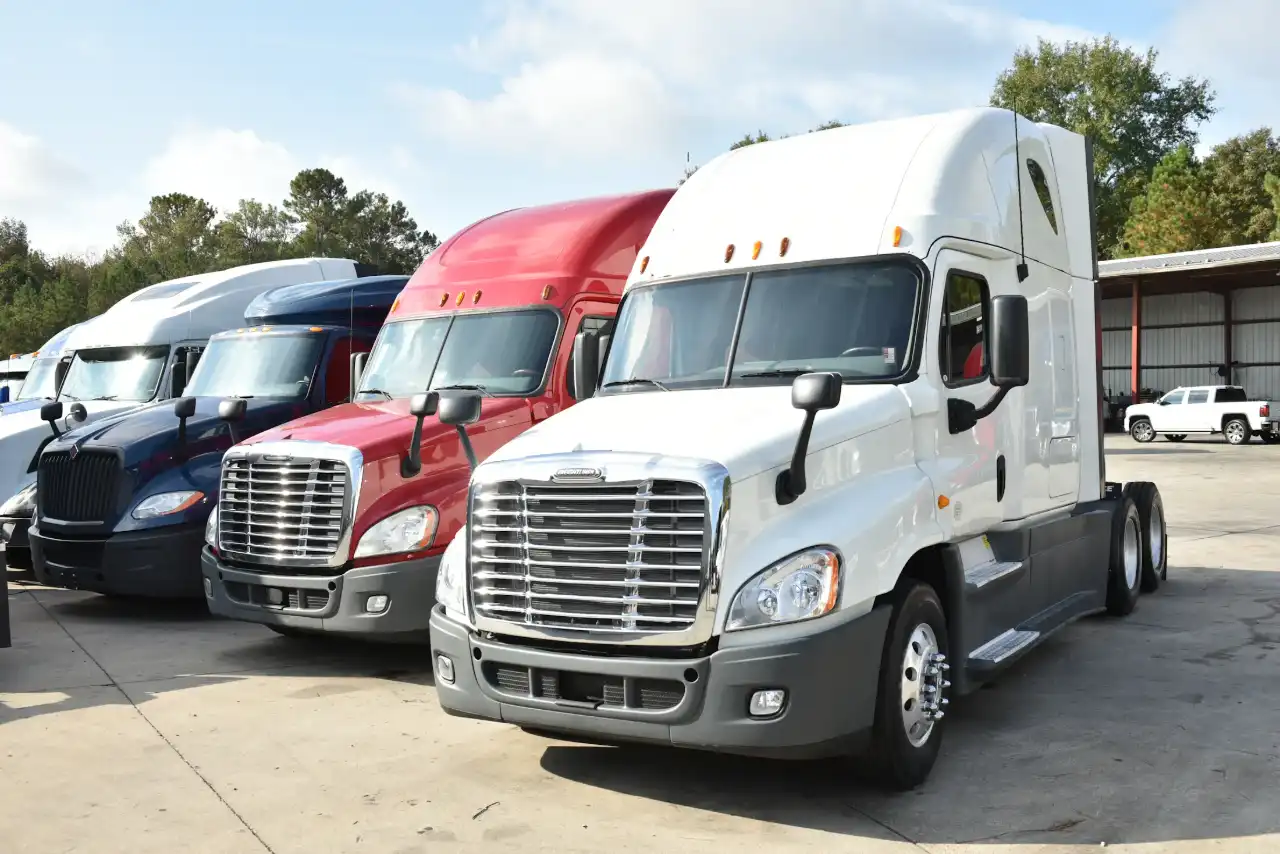
Understanding Your Truck’s Electrical System
Before diving into maintenance, it’s important to understand the key components of your truck’s electrical system.
- Battery – Stores electrical energy and provides power to the starter motor, ignition system, and other components when the engine is off.
- Alternator – Generates electrical power and recharges the battery while the engine is running.
- Starter Motor – Uses battery power to turn over the engine during startup.
- Wiring and Connectors – Carry electrical current to various systems, ensuring proper operation of lights, sensors, and controls.
- Fuses and Relays – Protect circuits from electrical overloads, preventing major damage to components.
Battery Maintenance
A weak or failing battery is one of the most common electrical problems in trucks. Proper maintenance can extend battery life and ensure reliable performance.
- Check voltage regularly – A fully charged battery should read between 12.6 and 12.8 volts when the truck is off. If the voltage drops below 12.4 volts, it may be time for a charge or replacement.
- Inspect for corrosion – Battery terminals can develop a buildup of corrosion, which can hinder electrical flow. Clean terminals with a wire brush and apply dielectric grease to prevent future buildup.
- Ensure tight connections – Loose battery cables can lead to intermittent electrical issues. Make sure all connections are secure.
- Monitor battery age – Most truck batteries last three to five years. If your battery is nearing the end of its lifespan, consider replacing it before it fails unexpectedly.
Alternator and Charging System Checks
Your alternator is critical in keeping the electrical system running by generating power and recharging the battery.
- Test the alternator output – A healthy alternator should produce between 13.8 and 14.5 volts while the engine is running. If it falls below this range, the alternator may not be charging the battery properly.
- Listen for unusual noises – A failing alternator may produce whining or grinding noises due to worn bearings.
- Check the drive belt – The alternator is powered by a serpentine belt. If the belt is loose or worn, the alternator won’t function properly. Inspect the belt for cracks, fraying, or slack.
- Look for warning lights – Most modern trucks have a battery or charging system warning light on the dashboard. If this light comes on, have the system checked immediately.
Wiring and Connection Inspections
Bad wiring can cause intermittent electrical problems that are frustrating to diagnose. Regular inspections can prevent issues before they start.
- Look for damaged or frayed wires – Wires that have been chewed by rodents, rubbed against sharp edges, or exposed to excessive heat can fail unexpectedly.
- Check grounding points – Poor grounding can cause electrical malfunctions. Make sure ground connections are clean and secure.
- Inspect for moisture intrusion – Water and electrical systems don’t mix. Look for signs of moisture in connectors and junction boxes, and use dielectric grease to prevent corrosion.
Preventing Overloads and Short Circuits
Electrical overloads and short circuits can cause major damage to your truck’s systems. Proper fuse and relay management can help prevent costly failures.
- Use the correct fuses – Never replace a fuse with one rated for a higher amperage. Doing so can lead to wiring damage or even a fire.
- Keep spare fuses and relays – Having extra fuses and relays on hand can save you from unnecessary downtime.
- Check for signs of burnt fuses – If a fuse blows repeatedly, it may indicate a deeper electrical issue that needs professional diagnosis.
Lighting and Accessory Maintenance
Your truck’s lighting system is crucial for safety, and accessory components such as power windows and radio connections rely on a stable electrical supply.
- Inspect headlights and taillights regularly – Replace dim or flickering bulbs before they fail completely.
- Check for water intrusion – Condensation inside light housings can lead to premature bulb failure.
- Test accessory power outlets – Many modern trucks use multiple power sources for auxiliary equipment. Ensure all outlets are working properly to avoid unexpected failures.
Regular Electrical System Testing
Routine electrical system testing can help you catch issues early before they become major problems.
- Perform load testing – A load tester can simulate the electrical demand of your truck’s systems and identify weak components.
- Check the voltage drop – High resistance in wiring can cause electrical problems. Testing for excessive voltage drop can pinpoint problem areas.
- Use a diagnostic scan tool – Many modern trucks have onboard diagnostics that can detect electrical faults before they cause a breakdown.
Keep Your Truck’s Power Flowing
Keeping your truck’s electrical system running smoothly requires regular maintenance, from battery care to wiring inspections. By staying proactive and addressing small issues, you can avoid breakdowns and keep your truck on the road.
If your truck needs electrical system maintenance in New Orleans, LA, contact 3R Diesel Repair today!